Ein Team des Lehrstuhls "Production Engineering of E-Mobility Components" (PEM) der RWTH Aachen hat die Antriebsbatterien von Tesla und dem chinesischen Elektroautohersteller BYD untersucht. Die Forschenden zerlegten die Akkus, verglichen ihre Eigenschaften und veröffentlichten die Ergebnisse in der Fachzeitschrift "Cell Reports Physical Science". Die Analyse zeigt, dass Teslas 4.680 Zellen vor allem auf eine hohe Energiedichte ausgelegt sind, während BYDs Blade-Zellen durch Volumeneffizienz und kostengünstigere Materialien punkten. Zudem ermöglicht die Bauweise der BYD-Batterie ein einfacheres Wärmemanagement, was laut Studie zu einer höheren Gesamteffizienz führt.
"Beide Hersteller haben bisher nur wenige Details zu ihren Batterien offengelegt, sodass viele mechanische Strukturen und Eigenschaften der Zellen bislang unbekannt waren", erklärt PEM-Leiter Prof. Achim Kampker. Generell gebe es nur wenige detaillierte Analysen moderner Elektrofahrzeug-Batterien.
- Studie zum Batterieleben von E-Autos: Erstaunlich langlebig
- Varta-Tochter: Porsche übernimmt Mehrheit
- E-Auto-Batterien: Fast wie neu nach einer Viertelmillion
Deshalb untersuchte das RWTH-Team die mechanische Konstruktion, die Abmessungen sowie die elektrischen und thermischen Eigenschaften der Zellen. Auch die Materialzusammensetzung der Elektroden, die Kosten der Zellmaterialien und die Fertigungsverfahren wurden analysiert. "Überraschend war, dass in den Anoden beider Batterien kein Silizium enthalten ist – besonders bei Tesla, da Silizium in der Forschung als Schlüsselmaterial zur Steigerung der Energiedichte gilt", so PEM-Prof. Heiner Heimes.
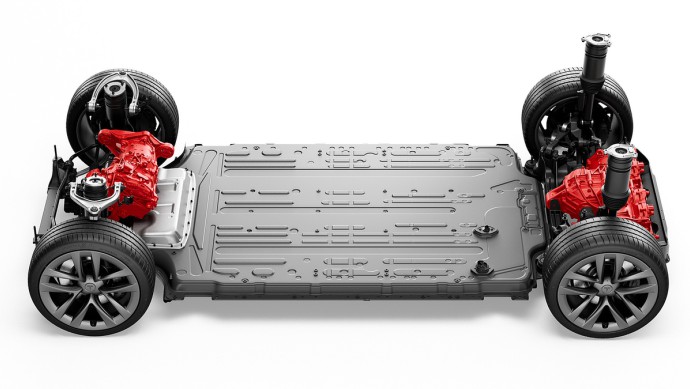
Ein weiterer zentraler Unterschied zeigt sich in der Lade- und Entladegeschwindigkeit. Hier setzt BYD auf eine besondere Technik: Die Lamination der Separator-Kanten fixiert Anoden und Kathoden im Elektrodenstapel optimal zueinander. Tesla hingegen verwendet ein neuartiges Bindemittel, das die aktiven Materialien in den Elektroden zusammenhält.
Trotz ihrer Unterschiede weisen die Batterien auch unerwartete Gemeinsamkeiten auf. Beide Hersteller setzen auf Laserschweißen zur Verbindung der dünnen Elektrodenfolien – eine bislang selten genutzte Technik, während am Markt üblicherweise Ultraschallschweißen eingesetzt wird. Zudem fällt auf, dass der Anteil der passiven Zellkomponenten wie Stromabnehmer, Gehäuse und Stromschienen trotz der deutlich größeren BYD-Zelle ähnlich hoch ist wie bei Tesla.
Auch interessant:
- Mercedes testet Feststoffzellen: Vierstellige E-Reichweiten in Sicht
- Batterie-Recycling: Sinnvoll – aber nicht vorhanden
- Batterie-Weltmarkt: Preise sinken unter magische Schwelle
"Weitere Untersuchungen sind nötig, um zusätzliche Parameter zu analysieren", sagt PEM-Experte und Hauptautor Jonas Gorsch. "Doch die aktuellen Ergebnisse liefern bereits eine wichtige Vergleichsbasis für großformatige Zelldesigns und bieten eine solide Grundlage für weitere Forschung und Optimierungen."